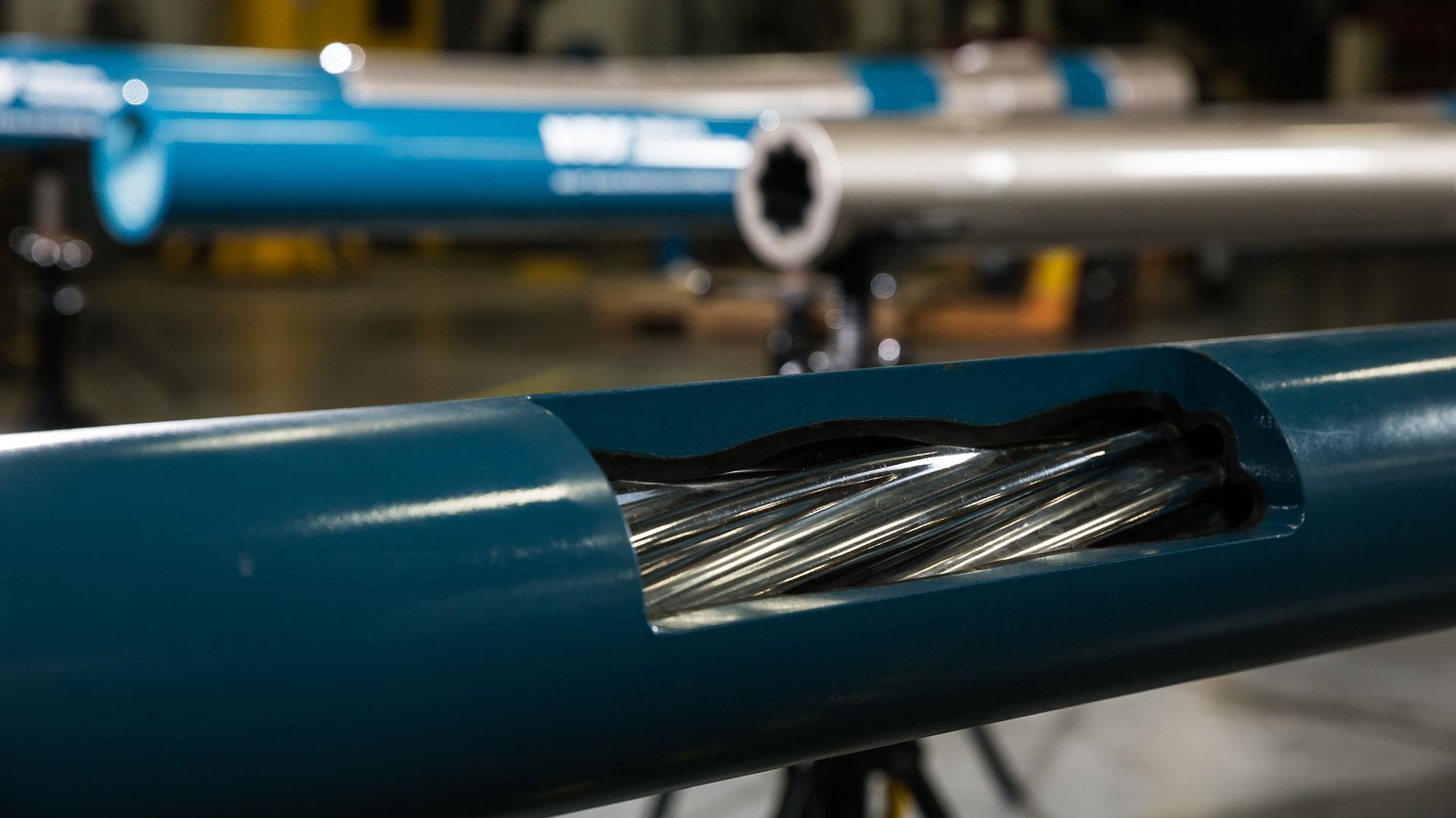
Drilling Mud Motor
What is a Drilling Motors?
- A drilling motor, often referred to as a mud motor drilling or downhole drilling motor, is a type of positive-displacement motor (PDM) used extensively in the oil and gas industry.
- It operates on hydraulic power, using drilling fluid (commonly called “drilling mud”) to create mechanical rotation.
- This rotation is used to drive a drill bit during drilling operations, especially in directional or horizontal drilling.
- The motor is located in the drill string, near the drill bit, and allows the bit to rotate while the rest of the drill pipe remains stationary
Benefits of Utilizing a Drilling Motors
Efficiency: Downhole motor directional can enhance the rate of penetration (ROP), reducing the overall drilling time.
Directional Drilling: HDD mud motors enable precise directional control, allowing the drilling path to be steered towards the target formation.
Flexibility: Downhole mud motor can be used in a variety of drilling situations, including vertical, horizontal, and directional drilling.
Reduced Wear and Tear: Since the drill string does not need to rotate, this can lead to reduced wear and tear on the drill pipe.
Cost-effective: Faster drilling rates and precise targeting can lead to reduced operational costs.
Environmental Benefits: More precise drilling can lead to less surface disruption and a smaller footprint, thereby reducing the environmental impact.
How to Use a Drilling Motors?
- The directional drilling motor is incorporated into the drill string and positioned near the drill bit.
- Mud motor directional drilling is then pumped down the drill string. As it passes through the motor, it drives an internal rotor, which in turn spins the drill bit.
- The speed of the drill bit is controlled by varying the flow rate of the drilling fluid.
- Directional control is achieved by adjusting the orientation of the HDD mud motors within the borehole.
What Can Users Do With Drilling Motors?
- Drilling motors enable users to perform directional drilling, including horizontal and curved paths, which is not feasible with traditional rotary drilling.
- Users can target specific geological formations, thereby increasing the success rate of oil and gas exploration.
- Downhole mud motor allows for the drilling of relief wells, used in efforts to control blowouts from oil wells.
- Downhole motor is used in underbalanced drilling, which can increase drilling speed and reduce formation damage.