Break-out units, also known as make/break machines, are critical components in tool service facilities, primarily utilized for assembling and disassembling tool joints. Adjusting the parameters on these units correctly can significantly improve operational efficiency, tool longevity, and safety. This guide explores essential adjustable parameters and accessories to help you maximize the effectiveness of your break-out unit.
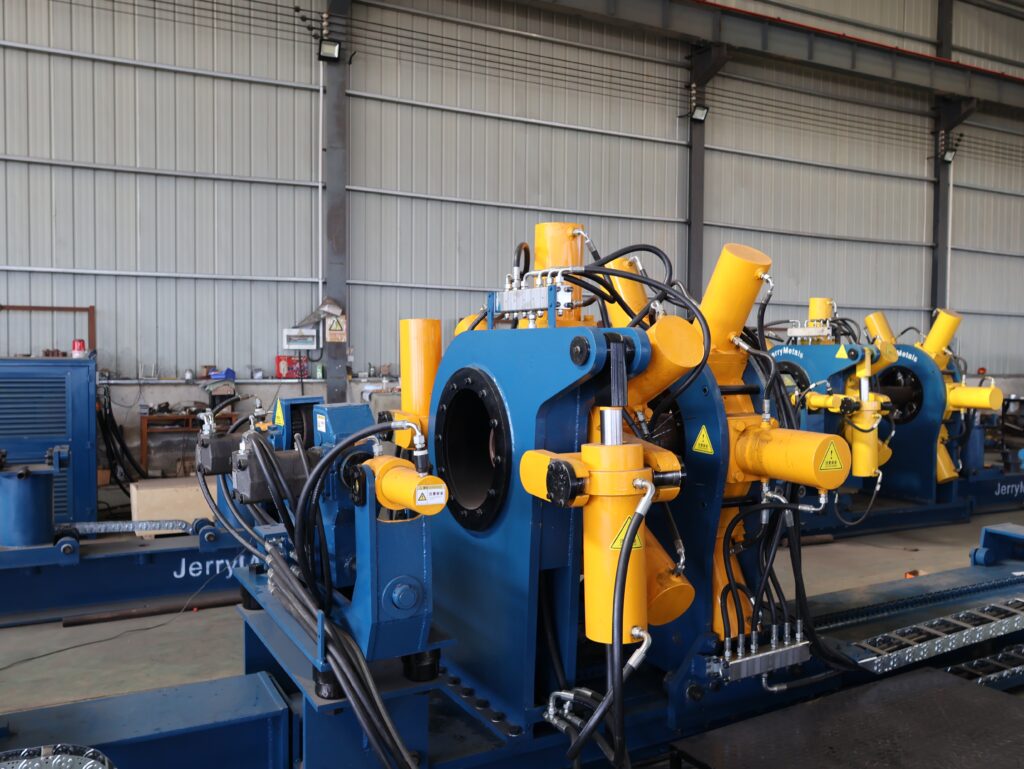
Adjustable Bed Length
The standard bed length on most break-out units is 16 feet, but customization options are available to meet specific workspace and handling needs. Longer or shorter bed lengths can be provided upon request, ensuring efficient space utilization and easier tool handling. Choosing the appropriate bed length minimizes operational downtime by accommodating tools of various sizes without unnecessary repositioning.
Extension Beams for Enhanced Versatility
Extension beams, available in lengths of 6, 10, 12, and 19 feet, can be easily bolted onto either side of the main bed. These beams extend functionality, accommodating accessories like hydraulic support jacks and push/pull assemblies. Utilizing these extension beams significantly reduces the need for external handling equipment, ensuring smoother workflow and enhanced safety in tool manipulation.
Hydraulic Support Jacks
Operable directly from the control console, hydraulic support jacks enhance the handling of heavy or complex workpieces. These jacks glide smoothly along the extension beams and secure in place with placement pins. The adjustable jacks, limited to a maximum of four per TorqueMaster unit, provide precise alignment and support, reducing the risk of tool damage or operator injury.
Push/Pull Assemblies
The hydraulic push/pull assembly facilitates efficient insertion and removal of rotors from stators, applying up to 60,000 lbf of pushing force and 40,000 lbf of pulling force. Operated via the console, this assembly reduces physical strain and increases operational safety. The integrated hydraulic gauge provides real-time force measurement, ensuring accuracy and consistency.
Tilt Cylinder for Push/Pull Assembly
To further streamline operations, the push/pull tilt cylinder allows the push/pull assembly to be effortlessly raised into working position or lowered when idle. This capability eliminates manual intervention and enhances operator safety by preventing reliance on overhead cranes or manual lifting.
Heavy-Duty Spinners
Designed for rapid connection handling, heavy-duty spinners manage tools ranging from 14” OD up to 32” OD. Mounted directly onto the headstock or tailstock, the spinner expedites the spinning process of low-torque shouldered connections. The controlled hydraulic spinning reduces wear on joints and accelerates the assembly/disassembly process.
Hose Chain Protection
Protective hose chains, available in metal or plastic, ensure longevity and safety of hydraulic hoses by enclosing them securely along the bed and extension beams. Not only does this reduce hose wear significantly, but it also mitigates tripping hazards, ensuring compliance with safety standards.
Digital Torque Logging Systems
Advanced torque logging systems, like the LogMaster™ series, provide precise torque monitoring via user-friendly touchscreens. These digital systems track and record torque operations, maintaining accuracy even in harsh working conditions, facilitating better process control and audit trails.
TrueTorque™ Digital Gauge
Replacing traditional hydraulic gauges, the TrueTorque™ digital gauge offers unparalleled accuracy within +/- 0.5%. Featuring an IPS screen, which has a higher brightness and is suitable for outside operation, this gauge displays real-time torque data, calibration history, machine usage, and operational temperatures. Such precision assists in compliance with quality assurance protocols and tool integrity checks.
Independent Clamp Control
Independent clamp control allows operators to fine-tune clamping pressure, essential for handling thin-walled or sensitive tools without causing damage. Additionally, it provides enhanced grip for hardened materials, significantly reducing slippage during torque operations.
Safety Enhancements
Safety features like polycarbonate shields provide critical protection against debris and tool fragments. Additionally, operational lights and actuator pin sensors clearly communicate machine readiness, reducing operational risks. Hose bridges further eliminate tripping hazards from exposed hydraulic hoses.
Integration with Jar Tester Control
Break-out units can also integrate seamlessly with NOV Jar Tester controls, removing the need for separate control consoles. This integration simplifies workspace setups and enhances operational efficiency.
Conclusion
Properly understanding and utilizing the adjustable parameters and accessories of break-out units can dramatically enhance operational efficiency, safety, and equipment longevity. Selecting the right combination of options tailored to your operational needs ensures optimal performance and maintains high standards of safety and quality in your tool service facility.
For detailed consultations and to tailor your break-out unit to your specific needs, contact our experts here →.